The cracking furnace is the basis of ethylene production, and fireproof material is an important factor, affecting the service life of the cracking furnace. In particular, The living and working group of the SRT cracking furnace uses refractory materials.
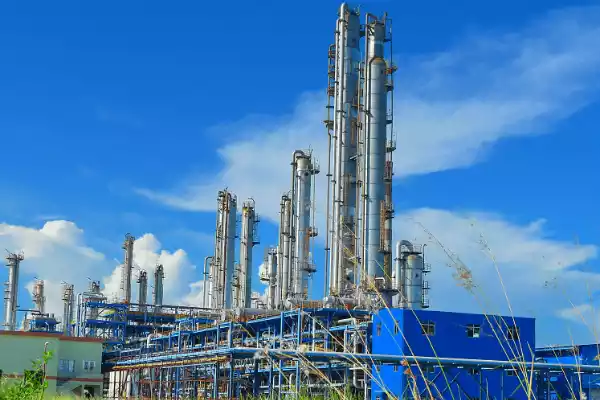
Cracking furnace SRT
Refractories for SRT cracking furnace
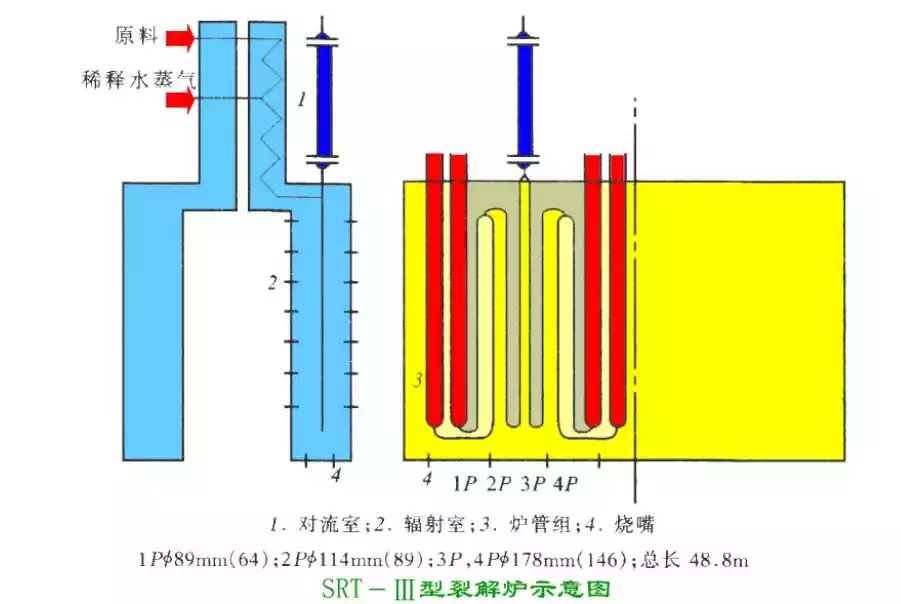
In the internal high-temperature zone of the cracking furnace, refractory bricks are used to make the walls and bottom of the furnace.
Refractory casting material:
Refractory castings are used to fill and repair small gaps and damaged parts of furnaces.
Used for oven insulation layer.
Insulating bricks are used in the outer zone of the pyrolysis furnace to reduce thermal conductivity and heat loss.
Thermal barrier coating:
The outer surfaces of the pyrolysis furnace are covered with a thermal protective coating. These coatings are usually made from ceramic fibers, refractory cement and other materials, which can provide better thermal insulation effect.
Ceramic fiber blanket
Temperature classification ℃ | 1140 | 1260 | 1400 | ||
Assessment | XT114 | XT126-A | XT126-B | XT140-A | XT140-B |
Constant linear change % ℃×24h | ≤-3 950 | ≤-3 1000 | ≤-3 1100 | ≤-3 1200 | ≤-3 1350 |
Thermal conductivity W/(m·K)500℃ | ≤0.153 | ||||
Tensile strength, MPa thickness 25 mm | >0.04 | >0.05 | >0.04 | >0.06 | |
Bulk density kg/m3 | 64/96/128/160 | ||||
Al2O3 % | ≥44 | ≥45 | ≥45 | ≥52 | ≥36 |
SiO2 % | ≥52 | ≥52 | ≥54 | ≥46 | ≥48 |
ZrO2 % | / | / | / | / | ≥15 |
Fe2O3 % | ≤1.0 | ≤0.8 | ≤0.2 | ≤0.2 | ≤0.1 |
Al2O3+SiO2 % | ≥96 | ≥97 | ≥99 | ≥99 | ≥ |
Al2O3+SiO2+ZrO2 % | / | / | / | / | 99 |
Size | 3600/7200×610×20/30/50 |
Plastic refractory
Subject | Silicon carbide | Zirconium Chrome Corundum | ||
NMK4 | NMK5 | NMK6 | NMK7 | |
Al2O3 % | / | / | / | ≥80 |
SiC % | ≥40 | ≥60 | ≥70 | / |
Cr2O3 % | / | / | / | ≥3 |
ZrO2 % | / | / | / | ≥2 |
Bulk density g/cm3 110℃×24h | ≥2.4 | ≥2.5 | ≥2.6 | ≥2.8 |
Constant linear change % 1000℃×3h | -0.4~0 | -0.5~0 | -0.6~0 | -0.6~0 |
Cold crush strength MPa 1000℃×3h | ≥60 | ≥70 | ≥80 | ≥90 |
Wear resistance at room temperature cm3 1000℃×3h | ≤7 | ≤6 | ≤5 | ≤5 |
Thermal shock stability cycle 1000℃ water cooling | ≥30 | ≥35 | ≥40 | ≥30 |
Plasticity index % | 15~55 | |||
Plasticity W/(m·K) 1000℃ | 3~5 | 5~7 | 6~8 | 2~3 |
Maximum operating temperature ℃ | 1400 | 1500 | 1600 | 1600 |
High alumina castable refractory
Index | High Alumina Castable | |
Al2o3% | 65 | |
Sio2 % | 30 | |
Cao % | 6 | |
Bulk density g/cm³ | 110℃,24h | 2.5 |
1350℃,24h | 2.6 | |
Cold flexural strength MPA | 110℃,24h | 6 |
1350℃,24h | 7.5 | |
Hot bending strength MPA | 110℃,24h | 45 |
1350℃,24h | 60 | |
1350 Rate of change of the burning line | 0.2 | |
Mixing water consumption % | 10-12% | |
Operating temperature | 1400 |